THIẾT KẾ QUY TRÌNH CÔNG NGHỆ GIA CÔNG CHI TIẾT CÀNG GẠT SỐ, đồ án môn học công nghệ chế tạo máy, bài tập lớn công nghệ chế tạo máy, thiết kế quy trình công nghệ gia công chi tiết
Thiết kế quá trình công nghệ gia công chi tiết: Càng Gạt Số
Trong điều kiện:
- Dạng sản xuất hàng loạt vừa.
- Trang thiết bị tự chọn.
Với các yêu cầu sau:
- PHẦN BẢN VẼ:
- Bản vẽ chi tiết gia công khổ giấy A0.
- Bản vẽ chi tiết lồng phôi khổ giấy A0.
- Bản vẽ sơ đồ nguyên lý khổ giấy A0.
- 02 bản vẽ kết cấu nguyên công khổ giấy A0.
- 01 bản vẽ đồ gá khổ giấy A0 (đối với CĐCNKTCK 02 bản).
- PHẦN THUYẾT MINH:
- Phân tích chi tiết gia công
- Chọn phôi, phương pháp chế tạo phôi và xác định lượng dư gia công.
- Lập bảng quy trình công nghệ gia công cơ
- Biện luận qui trình công nghệ.
- Thiết kế đồ gá.
- Kết luận về quá trình công nghệ
Ngày giao đề ……………, ngày hoàn thành ……………
Giám Hiệu duyệt Khoa Cơ khí GV hướng dẫn
Chương 1 : PHÂN TÍCH SẢN PHẨM
1 /Kết cấu.
Yêu cầu kĩ thuật quan trọng nhất là dung sai độ không song song giữa ø 15
và các mặt E,F≤0.05,độ không song song giũa mặt E và mặt F ≤0.05
1.2 /Phân tích vật liệu.
-Càng gạt số được chế tạo bằng gang dẻo GZ45-6
+GZ:ký hiệu gang dẻo
+45:giới hạn bền kéo ≤ 45kg/mm2.
+6:δ=6%
1.3/ Yêu cầu kỹ thuật.
1.3.1/ Kích thước.
1.3.1.1/ Các kích thước dung sai chỉ dẫn.
Kích thước lỗ : ø15+0.025.
KTDN:
IT: 0.025
ES:0.025
EI:0
=>CCX 7, miền dung sai H.
=> ø 15+0.025 => 15H7.
Kích thước 36±0.1
KTDN: 36
IT: 0.2
ES: 0.1
EI: 0.1
=>CCX 8,
Kích thước : 20±0.1
KTDN: 20
IT: 0.2
ES: 0.1
EI: 01.1
=>CCX 12
Kich thước : 13±0.1
IT: 0.2
ES: 0.1
EI: 0.1
=>CCX 12
Kích thước :15±0.1
IT: 0.2
ES: 0.1
EI: 0.1
=>CCX 12
Kích thước : 15±0.1
IT: 0.2
ES: 0.1
EI: 0.1
=>CCX 12
Kích thước :10±0.1
IT: 0.2
ES: 0.1
EI: 0.1
=>CCX 12
1.3.1.2/Kích thước không chỉ dẫn dung sai.
Kích thước giới hạn bởi hai bề mặt không gia công có CCX 16:
Kích thước 112:
ES=2.2
EI=2.2
=>112±2.2
Kích thước : ø25
ES=1.3
EI=1.3
=> ø25±1.3
Kích thước R24,
ES=1.9
EI=1.9
=>R39±1.9
Kích thước R39,
ES=1.6
EI=1.6
=>R24±1.6
Kích thước R49,
ES=2.2
EI=2.2
=>R49±2.2
Kích thước 23,
ES=1.3
EI=1.3
=>23±1.3
Kích thước 98,
ES=2.2
EI=2.2
=>98±2.2
Kích thước 42.5,
ES=1
EI=1
=>42.5±1
Kích thước 20,
ES=1.3
EI=1.3
=>20±1.3
1.3.1.3/Độ nhám bề mặt.
Lỗ Ф15 có Ra 2.5 =>Cấp 6
Mặt E,F co Ra 2.5 =>Cấp 6
các mặt:A,B,C,D,K,H,G co Rz40=> cấp 3
1.3.1.4/Cơ tính vật liệu.
-Do grafit là cụm bông tương đối thu gọn,đồng thời lượng grafit trong gang dẻo ít hơn các loại gang khác nên cơ tính của gang dẻo đạt được độ bền kéo tương đối cao (thấp hơn gang cầu nhưng cao hơn rất nhiều so với gang xám)đặc biệt là độ dẻo dai cao............................................
CHƯƠNG II: XÁC ĐỊNH PHƯƠNG PHÁP CHẾ TẠO PHÔI
2.1. Chọn phôi:
Vật liệu chế tạo càng gạt số là gang dẻo GZ45-6, nên ta chọn loại phôi đúc.
2.2. Chọn phương pháp đúc để chế tạo phôi
- Phương pháp đúc bằng khuôn kim loại :dùng để đúc kim loại và hợp kim màu có độ chính xác và độ nhẵn của phôi đúc rất cao thường dùng cho sản xuất hàng loạt lớn và hàng khối, mặt khác làm khuôn kim loại là rất đắt. Nên không thích hợp
- Phương pháp đúc ly tâm: Chỉ đúc được những sản phẩm có hình dáng tròn xoay thành ống mỏng nên không thích hợp.
- Phương pháp đúc bằng mẫu chảy: Dùng để đúc chi tiết có hình dáng rất phức tạp, việc làm mẫu chảy rất khó khăn và tốn kém vật liệu vì một mẫu chỉ đúc được một sản phẩm. Thường dùng cho sản xuất đơn chiếc. Nên không thích hợp.
- Phương pháp đúc bằng áp lực: Chủ yếu dùng để đúc kim loại và hợp kim màu nên không thích hợp.
- Phương pháp đúc trong khuôn cát: Đúc được tất cả các vật liệu có tính nóng chảy
- Thích hợp cho dạng sản xuất đơn chiếc hàng loạt nhỏ và hàng loạt vừa
- Đúc được những hình dạng phức tạp
- Vật liệu làm tròn khuôn CT3
- Vật liệu làm mẫu: maãu kim loaïi.
- Hỗn hợp làm khuôn : cát , đất sét ( chất kết dính ) vật liệu phụ, nước…
Cho nên rất thích hợp cho việc chế tạo phôi bằng gang, đô chính xác tương đối cao , phù hợp cho dạng sản xuất hàng loạt vừa
· Do đó ta chọn phương pháp đúc trong khuôn cát ,mẫu bằng kim loại khuôn bằng máy là thích hợp, phôi đúc đạt được chính xác cấp II
2.3.Tra lượng dư khi đúc.
- Kích thước lớn nhất của chi tiết là 112
- Tra bảng lượng dư gia công cơ và dung sai kích thước danh nghĩa của vât đúc là gang cấp chính xác II có:
+ Kích thước 36
Lượng dư khi đúc 2.5±0.5
CHƯƠNG III : BIỆN LUẬN NGUYÊN CÔNG
3.1/Nguyên công I.
-Làm sạch cát còn bám lại trên bầ mặt chi tiết sau khi đúc.
-Mài những phần đậu rót, đậu ngót do chế tạo phôi để lại.
-Kiểm tra các kích thước cần đạt sau khi đúc.
-Kiểm tra các lỗ khí, nứt
3.2/Nguyên công II: Phay thô đồng thời 3 mặt đầu
3.2.1.Biện luận về nguyên công:.....................................................................................................
5.2.1Tính toán sai số
5.2.2Tính sai số chuẩn
Sai số chuẩn ec xuất hiện trong quá trình định vị phôi trên đồ gá và có giá trị bằng khoảng giao động kích thước từ chuẩn đo tới mặt chốt tỳ theo phương kích thước gia công ( trong phần lớn trường hợp được lấy bằng dung sai của kích thước này )
Ở đây do gốc kích thước trùng với chuẩn định vị nên sai số chuẩn bằng 0.
5.2.3Sai số kẹp chặt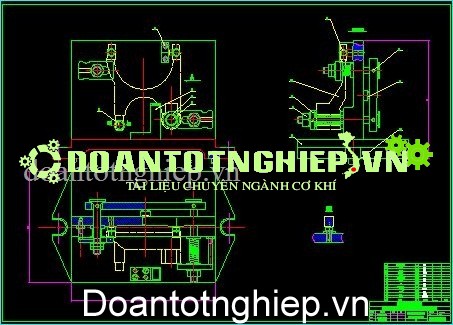
Là sai số do lực kẹp gây ra vì phương của lực kẹp vuông góc với phương của kích thước gia công nên nó không ảnh hưởng đến độ chính xác của bề mặt gia công, do đó nên sai số kẹp chặt ek =0.
5.5.7Sai số mòn
Trong quá trình tháo lắp chi tiết nhiều lần bề mặt chi tiết định vị bị mòn do đó phát sinh sai số mòn em. Và nó được tính theo công thức
MỤC LỤC
LỜI NÓI ĐẦU.. 3
Chương 1 : PHÂN TÍCH SẢN PHẨM... 4
1 /Kết cấu. 4
1.2 /Phân tích vật liệu. 4
1.3/ Yêu cầu kỹ thuật. 4
1.3.1/ Kích thước. 4
1.3.1.1/ Các kích thước dung sai chỉ dẫn. 4
1.3.1.2/Kích thước không chỉ dẫn dung sai. 5
1.3.1.3/Độ nhám bề mặt. 6
1.3.1.4/Cơ tính vật liệu. 6
CHƯƠNG II: XÁC ĐỊNH PHƯƠNG PHÁP CHẾ TẠO PHÔI 6
2.1. Chọn phôi: 6
2.2. Chọn phương pháp đúc để chế tạo phôi 6
2.3.Tra lượng dư khi đúc. 7
2.4. Tính hệ số sự dụng vật liệu và khối lượng chi tiết gia công: 7
CHƯƠNG III : BIỆN LUẬN NGUYÊN CÔNG.. 9
3.1/Nguyên công I. 9
3.2/Nguyên công II: Phay thô đồng thời 3 mặt đầu. 9
3.2.1.Biện luận về nguyên công: 10
3.2.2.Về kích thước : 10
3.2.3. Biện luận về chọn chuẩn gia công : 10
3.2.4.Bie^.n lua^.n ve^` my. 10
3.2.5.Biện luận về chọn dao : 10
3.2.6. Đồ gá : 11
3.3/Nguyên công III: Phay thô dồng thời 3 mặt day. 11
3.3.1.Biện luận về thứ tự gia công : 11
3.3.2.Về kích thước : 11
3.3.3. Biện luận về chọn chuẩn gia công : 11
3.3.4.Bie^.n lua^.n ve^` my. 11
3.3.5.Biện luận về chọn dao : 12
3.3.6. Đồ gá : 12
3.4/Nguyên công IV: khoan,khoét,doa lỗ Ø15. 12
3.4. 5.Biện luận về dao: 13
3.4.6.Đồ gá: 13
3.5/Nguyên công V: Phay thô đồng thời 2 mặt E,F. 13
3.5.5.Biện luận về dao: 14
3.5. 6.Đồ gá: 14
3.6/Nguyên công VI: Phay thô mặt G.. 15
3.6.1 .Biện luận về thứ tự gia công : 15
3.6.2.Về kích thước : 15
3.6.3. Biện luận về chọn chuẩn gia công : 15
3.6.4. Biện luận về chọn máy : 15
3.6.5.Biện luận về dao: 16
3.6. 6.Đồ gá: 16
3.7/ Nguyên công:Phay tinh đồng thời E,F. 16
3.7.1 .Biện luận về thứ tự gia công : 16
3.7.2.Về kích thước : 16
3.7.3Biện luận về chọn chuẩn gia công : 16
3.7.4. Biện luận về chọn máy : 17
3.7. 5.Biện luận về dao: 17
3.7.6.Đồ gá: 17
3.8/Nguyên công VIII: phay thô mặt K.. 17
3.8.1.Biện luân thứ tự nguyên công. 18
3.8.2.Về kích thước. 18
3.8.3.Biện luận chuẩn gia công. 18
3.8.4.Biện luận về máy. 18
3.8.5.Biện luân về dao.. 19
3.8.6.Đồ gá :Chuyên dùng. 19
3.9/Nguyên công IX: Phay thô đồng thời 3 mặt B,C,D.. 19
3.9.1.Biện luận thứ tự nguyên công. 19
3.9.2.Về kích thước. 19
3.9.3.Biện luận về chuẩn gia công. 19
- 3.9.4.Biện luận về máy. 19
3.9.5.Biện luận về dao. 20
3.9.6.Đồ gá. 20
3.10/Nguyên công X: phay thô mặt A.. 20
3.10.1.Biện luận thứ tự nguyên công. 20
3.10.2.Về kích thước. 20
3.10.3.Biện luận về chuẩn gia công. 20
3.10. 4.Biện luận về máy. 20
3.10.5.Biện luận về dao. 21
3.10.6.Đồ gá. 21
3.11/Nguyên công XI:phay thô mặt H.. 21
3.11.1.Biện luận thứ tự nguyên công. 21
3.11.2.Về kích thước. 21
3.11.3.Biện luận về chuẩn gia công. 21
3.11.4.Biện luận về máy. 22
3.11.5.Biện luận về dao. 22
3.11.6.Đồ gá. 22
3.12/Nguyên công XII:khoan,taro M10x1.5. 22
3.12.1.Biện luận thứ tự nguyên công. 22
3.12.2.Về kích thước. 22
3.12.3.Biện luận về chuẩn gia công. 22
3.12.4.Biện luận về máy. 23
3.12.5.Biện luận về dao. 23
3.12.6.Đồ gá. 23
3.13/Nguyên công XIII : Tổng kiểm tra. 23
Chương IV: TÍNH CHẾ ĐỘ CẮT. 24
4.1/ Tính chế độ cắt nguyên công II : Phay đồng thởi mặt đầu. 24
4.2/ Tính chế độ cắt nguyên công III : Phay thô đồng thời 3 mặt đáy. 26
4.3/Tính chế độ cắt nguyên công IV : khoan,khoét,doa Ø15. 27
4.4/Tính chế độ cắt nguyên công V : Phay thô đồng thời mặt E,F. 29
4.5/Tính chế độ cắt nguyên công VI : Phay mặt G.. 31
4.6/Tính chế độ cắt nguyên công VII : Phay tinh đồng thời mặt E,F. 32
4.7/Tính chế độ cắt nguyên công VIII : Phay mặt K.. 33
4.8/Tính chế độ cắt nguyên công IX:phay 3 mặt B,C,D.. 34
4.9/Tính chế độ cắt nguyên công X : Phay mặt A.. 35
4.10/Tính chế độ cắt nguyên công XI : Phay mặt H.. 36
4.11/Tính chế độ cắt nguyên công XII : khoan,taro Mx1.5. 37
Chương V: TÍNH TOÁN ĐỒ GÁ.. 39
5.1ĐỒ GÁ PHAY MẶT H.. 39
5.1.1 Lập sơ đồ gá đặt 39
5.1.2 Tính lực kẹp. 40
5.1.3 chọn cơ cấu kẹp theo lực kẹp. 40
5.1.4 Tính toán sai số. 41
5.1.4.1 Tính sai số chuẩn. 41
5.1.4.2 Sai số kẹp chặt 41
5.1.4.3 Sai số mòn. 42
5.1.4.4 Tính sai số điều chỉnh. 42
5.1.4.5 Tính sai số gá đặt 42
5.1.4.6 Sai số của đồ gá. 42
5.1.4. Yêu cầu kỹ thuật của đồ gá. 42
5.2 ĐỒ GÁ KHOAN ,TARO LỖ M10x1.5. 42
5.2.1 Lập sơ đồ gá đặt 42
5.2.2 Tính lực kẹp. 43
5.2.3 chọn cơ cấu kẹp theo lực kẹp. 43
5.2.4 Tính toán sai số. 44
5.2.5 Tính sai số chuẩn. 44
5.2.6 Sai số kẹp chặt 44
5.5.7 Sai số mòn. 45
5.2.8 Tính sai số điều chỉnh. 45
5.2.9 Tính sai số gá đặt 45
5.2.10 sai số của đồ gá. 45
5.2.11 êu cầu kỹ thuật của đồ gá. 45
5.3 KẾT LUẬN.. 45
5.4 TÀI LIỆU THAM KHẢO.. 46
.
THIẾT KẾ QUY TRÌNH CÔNG NGHỆ GIA CÔNG CHI TIẾT CÀNG GẠT SỐ, đồ án môn học công nghệ chế tạo máy, bài tập lớn công nghệ chế tạo máy, thiết kế quy trình công nghệ gia công chi tiết